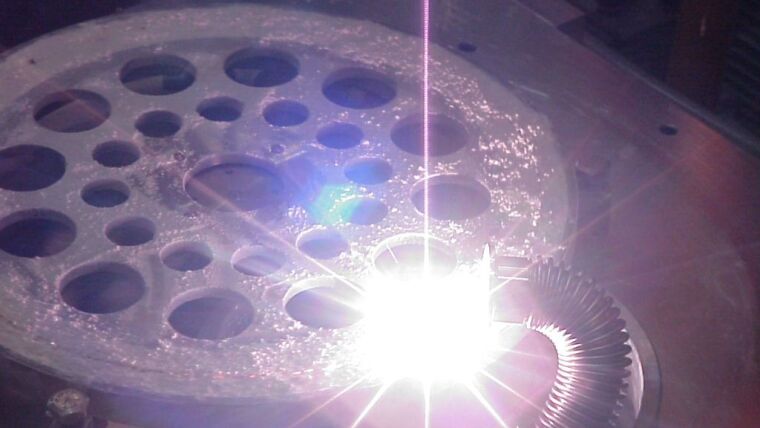
Laser-induced Periodic Surface Structures (LIPSS)
Image: CSI/FSULaser-induced Periodic Surface Structure (LIPSS)
Another subject of current research is the generation of laser-induced periodic surface structures (LIPSS) by means of ultrashort pulse lasers. LIPSS are formed on the material surface in the focus spot as a result of the interaction with the pulsed laser radiation. The periodic structures are of the same order of magnitude as the wavelength of the laser radiation used, their orientation being determined to a large extent by the direction of polarization. Therefore, a major focus of the investigations is to influence the formation of LIPSS structures on metals, glasses, ceramics, polymers and composites by the defined control of various laser and process parameters (e.g. laser wavelength, polarization state and laser fluence).
http://dx.doi.org/10.1016/j.apsusc.2015.01.056External link
A major focus of the investigations is therefore to influence the formation of LIPSS structures on metals, glasses, ceramics, polymers and composites via the defined control of a wide range of laser and process parameters (e.g. laser wavelength, polarization state and laser fluence) and thus to optimize them for potential applications.
An important basis for this is the fundamental understanding of the formation process of the different LIPSS types, which is still controversially discussed in the literature. A comprehensive summary of the available theories and model ideas was recently published in Laser & Photonics Reviews.
https://doi.org/10.1002/lpor.202000215External link
LIPSS formation results in surfaces with a defined, nanoscale topography, which, in interaction with the chemical properties, results in a variety of functional properties. In addition to a modified absorption, transmission and reflection behavior of the surface, the LIPSS lead to specific structural colors resulting from the diffractive properties of the lattice-like surface structures. Thus, depending on the structure size, it is relatively easy to create anti-reflective surfaces or to secure products against counterfeiting.
Surfaces structured with LIPSS are characterized by a different wetting behavior compared to the original substrate. Strongly wetting, superhydrophilic surfaces are used, for example, for water extraction, whereas the self-cleaning effect also known from the lotus leaf is used for strongly wetting, superhydrophobic surfaces. A main focus of the research group is the generation of defined wetting states (structure gradients, hierarchical structures) in order to realize a directed liquid transport for example for applications in microfluidics (Lab on a Chip).
Gerichtete Flüssigkeitstransport basierend auf Gradientenstrukturen
Video: University of JenaGerichtete Flüssigkeitstransport basierend auf Leidenfrost-Effekt
Video: University of JenaZnO coating of a carbon fiber by PLD; Appl. Surf. Sci. 399 (2017) 282-287
Image: CSI/FSUPulsed Laser Deposition (PLD)
The PLD process offers a flexible and versatile method of applying functional coatings to any substrate material. With the help of a focused laser beam, the target material is ablated, converted to the plasma state and deposited on an opposite substrate. The main focus of the investigations is the generation of crystalline and amorphous metal oxide layers (e.g. TiO2, ZnO) on smooth and structured surfaces as well as textiles. This allows new approaches for the development of textile dye solar cells or catalytically active textile structures.
Pulsed Laser Deposition (PLD) - System
Image: CSI/FSUFor this purpose, a powerful Q-switched CO2 laser is used as an energy source, since infrared laser radiation is particularly suitable for ablating ceramic materials. In principle, the coating can be performed under ultra-high vacuum as well as under specific atmospheres (inert and reactive gases). The PLD test facility is equipped with a substrate heater operated with a separate CO2 laser and allows the MAPLE process (Matrix-Assisted Pulsed Laser Evaporation) to be carried out via a nitrogen-cooled target holder. This process can be used to deposit nanoparticles, polymers and biological materials, for example.